By Sai Karthik Kalvapalli
Autonomous Mobile Robots (AMR) are becoming commonplace in the manufacturing and warehouse spaces. Parallel to this phenomenon, the complexity of the applications is also increasing. The AMRs are expected to integrate into existing workflows in highly dynamic operating conditions. In these challenging environments, the Autonomy Software of the vehicle is tasked with driving the vehicle safely and simultaneously, enhancing operating efficiencies.
This can be viewed as a vehicle “Driving Policy” problem. Driving Policy can be loosely defined as a Software Module that continuously makes decisions such as whether to stop the vehicle for an obstacle/uncertain environment, slow down the speed or overtake another vehicle etc. The robot can be programmed to handle ambiguous conditions predictably. For example, the locations where the lanes are very narrow can be marked as “Low-Speed Zones”. Similarly, other such customisations specific to the operating conditions local to certain sections of a map can be handled. But there are so many scenarios, where such a simple workflow may not be good enough.
Challenging Operating Scenarios Encountered:
- A typically non-congested area becomes congested or there are certain areas where the operating conditions differ during various points in a day.
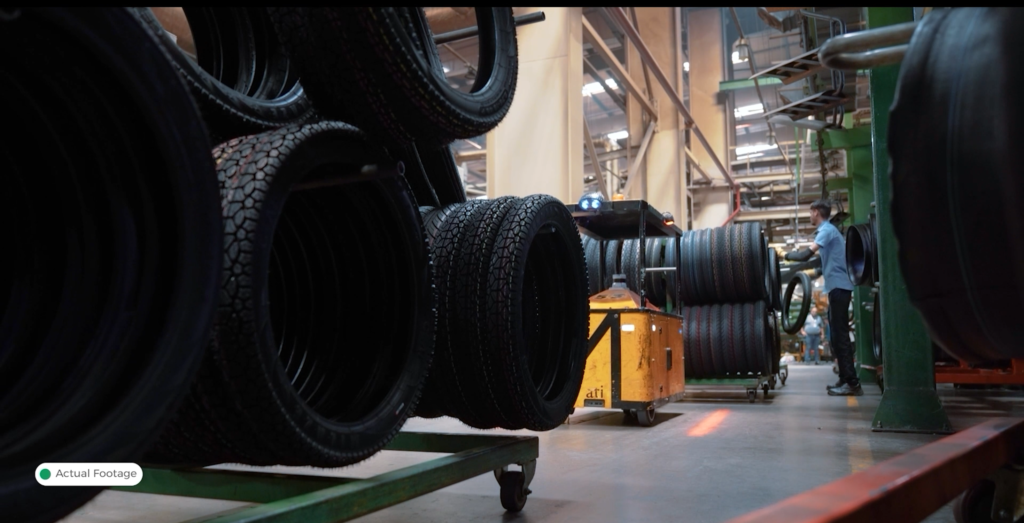
2. The flooring condition may suddenly change like a slippery floor on a rainy day, or some damage on the floor which makes running at low speed the only option, until it is fixed.
3. Reduced visibility due to weather conditions or some other reason.
4. “Scaling problem” on very large factory floors, where it would be difficult to designate all the segments manually as “Low-Speed Zones” or “High-Speed Zones”.
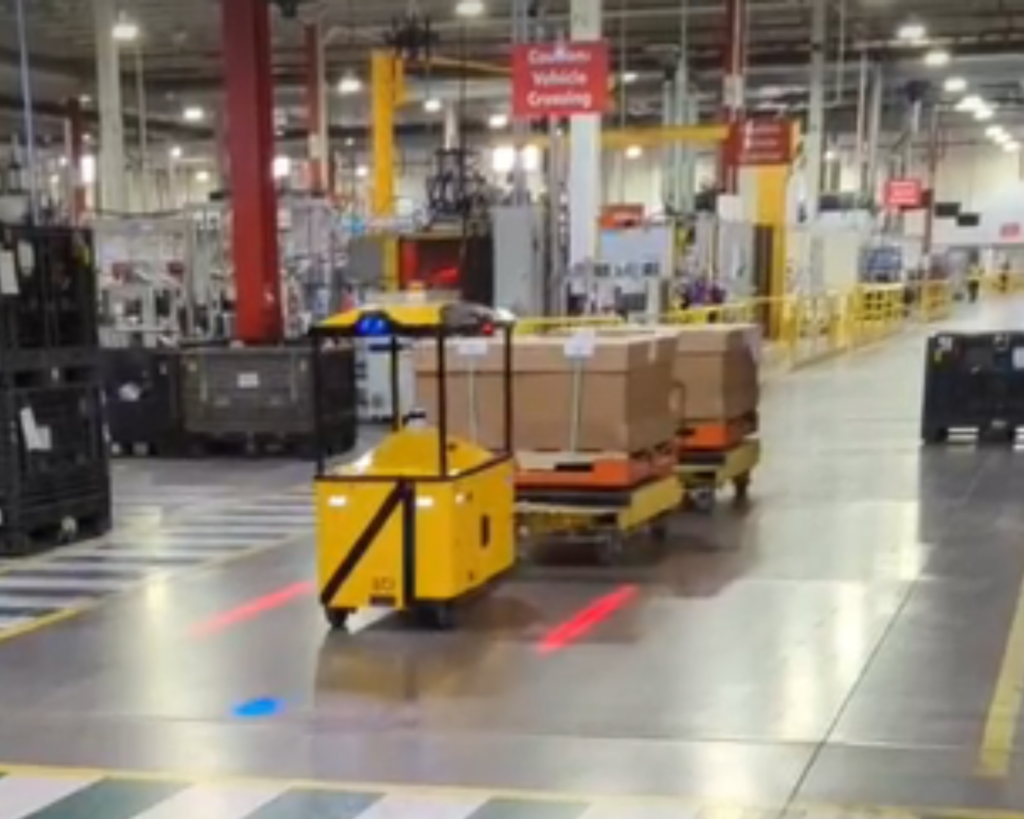
While operating in dynamic environments as above, the driving policy of the AMRs has to be flexible and adaptive. Vision or LiDAR data-based AI models are compelling in solving this problem. The AI models can be trained to detect such anomalous operating conditions. We have built a unified Neural Net model to detect a variety of conditions with camera and LiDAR data from diverse operating conditions of automotive factory shop floors, semi-public roads in factory campuses, and polymer manufacturing facilities.
The model inputs had to be multimodal from the get-go because of the relative merits of the individual sensor’s measurements. This in turn lead to robust decision-making in diverse scenarios. So the final trained model is capable of detecting multiple scenarios of wet floors in both indoor and outdoor scenarios, operating environments with a lot of movement around and cluttered spaces. Fine-tuning the model was primarily to reduce the false positive rate which tends to be seen in changing lighting conditions.
On the other hand, we also had to carefully balance the false-negative predictions while training as that has safety implications inference made by the trained models can be used by Ati’s Driving Policy module to adjust the driving behaviour dynamically. Such a “Smart Driving Policy” will enhance the safety of AMR operations and also improve the operating efficiencies of the fleet.